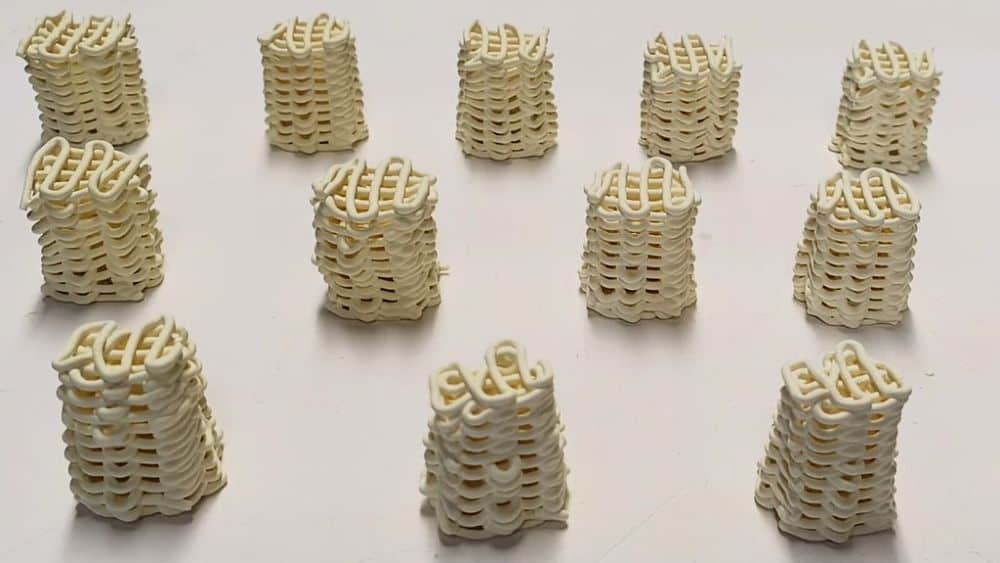
[Image above] Example of the 3D-printed indium oxide monoliths that University of Bath researchers created to remove PFAS from aquatic environments. Credit: Martins et al., Chemical Engineering Journal (CC BY 4.0)
This year, the fight against toxic “forever chemicals” scored an important victory when the U.S. Environmental Protection Agency (EPA) issued the first legally enforceable national drinking water standards for several common types of per- and polyfluoroalkyl substances (PFAS) in April 2024. This announcement could not have come at a better time considering that just three months later, researchers at the University of Birmingham proved indisputably that a wide range of PFAS can enter the body through the skin, which previously was considered impossible.
But even with this new regulation in place, taking the next step to remove PFAS from our water remains a herculean challenge.
Landfilling is a main way to deal with PFAS waste, but this method cannot be used to remove PFAS in our water supplies. In fact, it can contribute to the problem of PFAS in aquatic environments when these toxic substances leach from the waste into the ground.
Scientists have explored using advanced oxidation processes, such as photodegradation and electrochemical treatment, to directly degrade PFAS in water. But so far, these approaches are either unable to completely degrade PFAS or are too costly for industrial-scale implementation.
Currently, sorbents followed by incineration is the main strategy for aquatic PFAS removal. This strategy typically involves using activated carbon to adsorb PFAS and then placing the loaded molecules in a furnace to break down the PFAS with heat. (Though whether this process destroys PFAS or simply releases noxious residuals into the atmosphere is up for debate.)
Despite its popularity, there are several downsides to using activated carbon as the adsorbent. For one, this material does not adsorb short-chain PFAS well. Plus, it is susceptible to oxidation at elevated temperatures, which means it cannot be reused after incineration.
Metal oxide adsorbents may be a better option for PFAS removal due to their high-temperature stability, which allows reuse after thermal treatment. But to date, studies on metal oxides for PFAS removal have focused on the materials’ photocatalytic rather than adsorbent properties, so their ability to effectively adsorb PFAS is unknown.
In 2022, researchers at Hohai University in China published a paper that found indium oxide, which is known for its highly efficient photocatalytic removal of some PFAS, appeared to have good adsorption capacity as well. Based on this finding, researchers at the University of Bath in the U.K. decided to investigate further the potential of indium oxide to serve as an adsorbent for short-chain PFAS.
To investigate this potential, the researchers first had to decide which form of indium oxide to use for experiments. A previous study led by researchers at the University at Albany in New York achieved good degradation of PFAS with indium oxide nanoparticle slurries. But using nanoparticle slurries is challenging for large-scale applications due to the need for additional steps to prevent nanoparticle leaching.
Instead, the researchers decided to create a self-supported structure to allow for easy transport and removal while maintaining a high surface area. They accomplished this feat via extrusion-based 3D printing.
As explained in an open-access paper, they deposited a special ink consisting of indium oxide powder and a polymeric binder in a latticed monolith pattern. They then dried the structure at room temperature for 12 hours before sintering it at 500°C for 10 hours in air.
They tested the ceramic monolith’s adsorption capabilities using perfluorooctanoic acid (PFOA), one of the most prevalent PFAS chemicals. Initially, the monolith achieved a 53% removal rate of PFOA in a recirculating flow system. But following a low-temperature (500°C) pyrolysis process, the monoliths achieved a 75% removal rate in subsequent tests.
The researchers are unsure why the monoliths achieved a higher removal efficiency after thermal treatment. They posit it may be associated with an increase in the number of active sites following pyrolysis, but the mechanism will need to be confirmed in future studies.
In a press release, coauthor Garyfalia (Liana) Zoumpouli, research associate in the University of Bath’s Department of Chemical Engineering, says the results of this study are “very exciting,” and the ceramic monolith is “something we are keen to develop further and see in use.”
The open-access paper, published in Chemical Engineering Journal, is “3D-printed indium oxide monoliths for PFAS removal” (DOI: 10.1016/j.cej.2024.154366).